Компания, занимающаяся эргономикой, использовала 3D-сканеры SHINING 3D для сбора трехмерных данных и с помощью Solid Edge определила проектные данные для изготовления чехла обшивки сиденья, что быстро и эффективно облегчило последующие модификации.
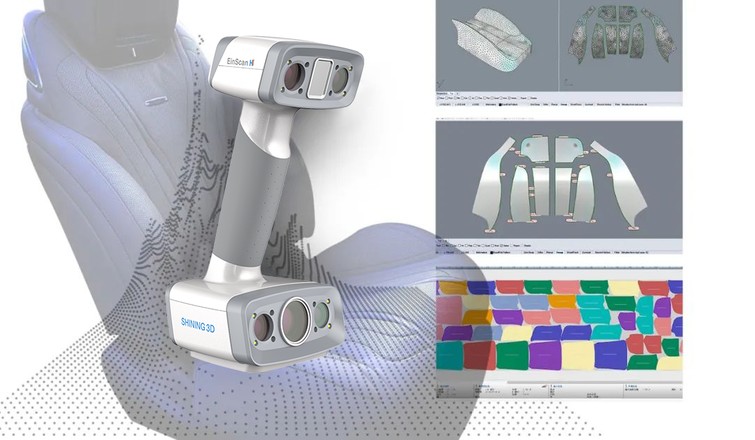
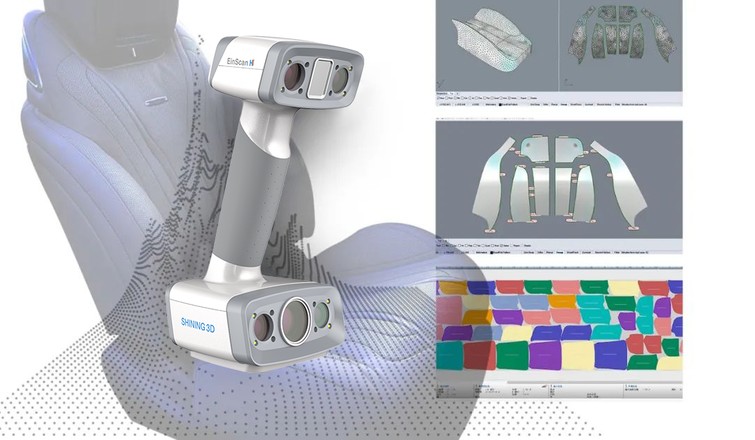
Бесспорно, потребители обращают внимание не только на практические характеристики товаров, но и внешний вид покупки также является одним из важных показателей, к сиденьям это тоже относится.
Однако мало кто знает, какие огромные усилия затрачиваются на создание чехлов для сидений. Теперь, с растущей тенденцией к созданию устойчивых, настраиваемых и легко изготавливаемых чехлов для сидений, производителям имеет смысл обратиться к эффективным решениям 3D-сканирования.
Именно так и поступила компания LeaTech. Компания Beijing Lea Tech Co. Ltd. занимается 3D-технологиями и эргономикой человека, и их система 3D-сканирования швов для сидений может использоваться в автомобильных сиденьях и мебели, а также в композитных материалах и изделиях для наружного применения. Чтобы улучшить рабочий процесс, компания LeaTech начала внедрять в свое производство 3D-сканеры EinScan компании SHINING 3D.
Contents
3D-сканер EinScan избавляет от длительного процесса ручной формовки
Производство чехлов для сидений постоянно развивается, но все еще остается в традициях ручного изготовления лекал. Традиционный дизайн чехла ручной работы должен пройти минимум 8 процессов и не менее 3 раундов утверждения внешнего вида, прежде чем его можно будет использовать для официального производства. Этот процесс может занять от нескольких дней до пары недель. Одним словом, ручное изготовление выкройки чехла для сиденья слишком зависит от прототипов, а процесс разработки не связан, неэффективен и не способен быстро реагировать на рынок.
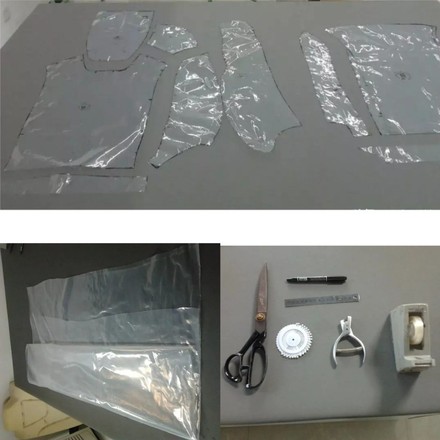
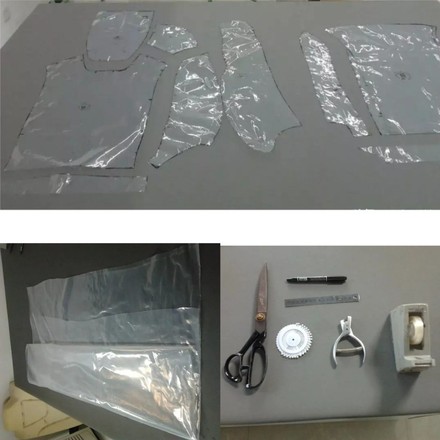
Как же производителю оптимизировать процесс изготовления лекал для современных чехлов для сидений?
Появление 3D-оцифровки дает ответ. Компании LeaTech и SHINING 3D совместно создали новое решение для проектирования чехлов сидений с использованием технологии цифрового 3D-сканирования – 3D Flatten Seam Development System.
Система требует всего 4 шага для завершения проектирования и разработки чехла сиденья и запуска его в производство.
Шаг 1: 3D сканирование/3D модели
Для получения 3D-данных компания LeaTech выбрала ручной 3D-сканер EinScan H с гибридным источником света. Благодаря большому диапазону сканирования 420*440 мм и впечатляющему высокому разрешению до 0,25 мм, 3D-сканер EinScan H поддерживает получение мелких деталей и быстрое сканирование, ускоряя рабочий процесс и повышая эффективность изготовления деталей.
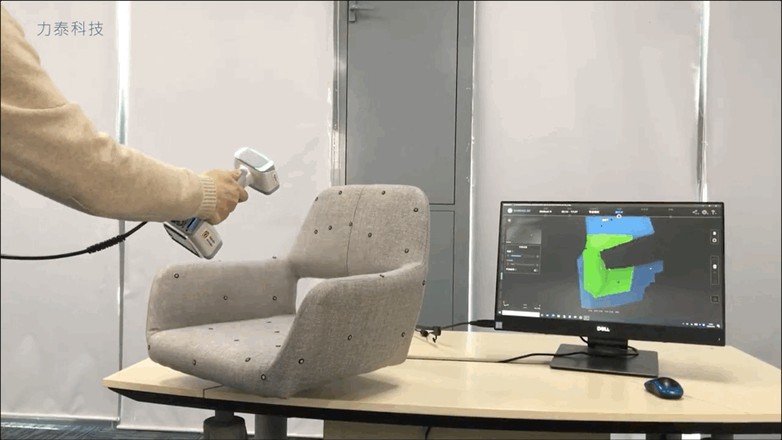
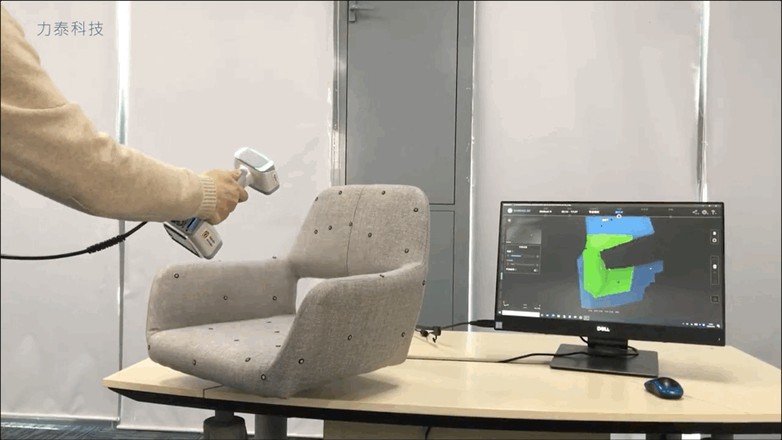
Шаг 2: Определите шов
Оптимизация 3D-модели и определение листа раскроя в Geomagic Essentials автоматически устраняет границы поверхности и сглаживает ее.
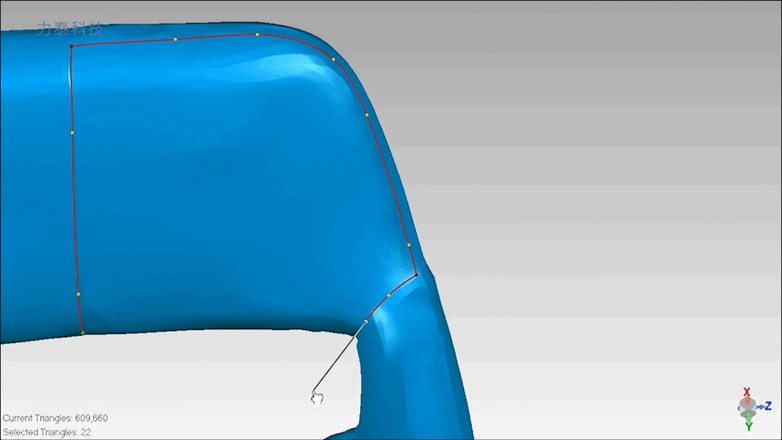
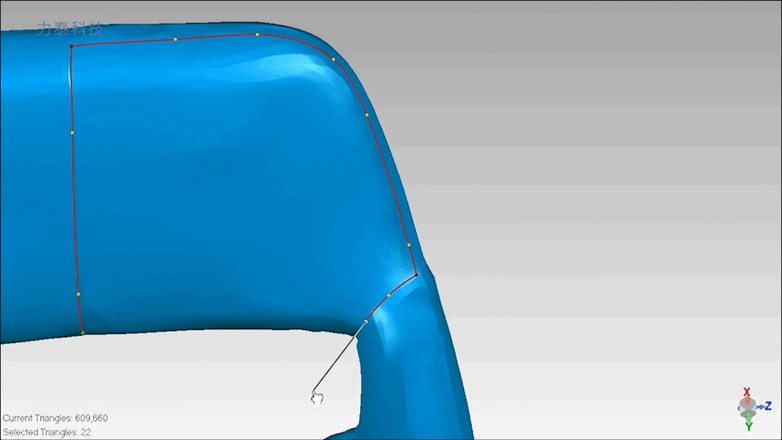
Шаг 3: Автоматическое разворачивание 2D-детали
Быстрое разворачивание вырезанных 2D-деталей. Можно задать параметры для устранения натяжения и морщин и оптимизации формы вырезанного листа.
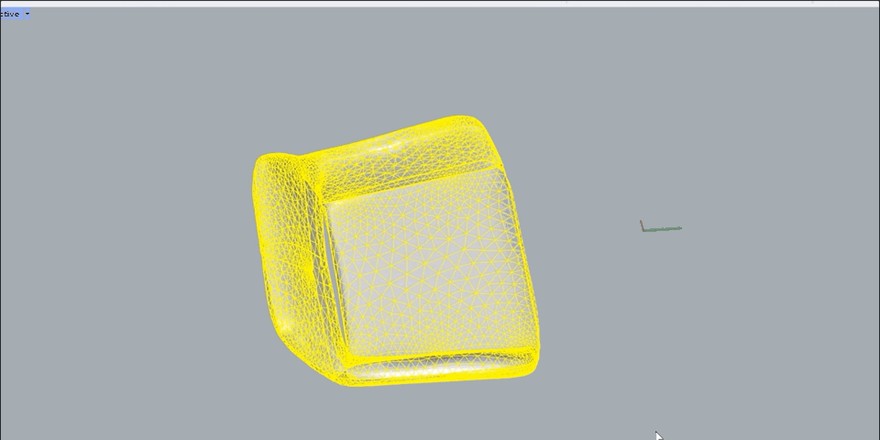
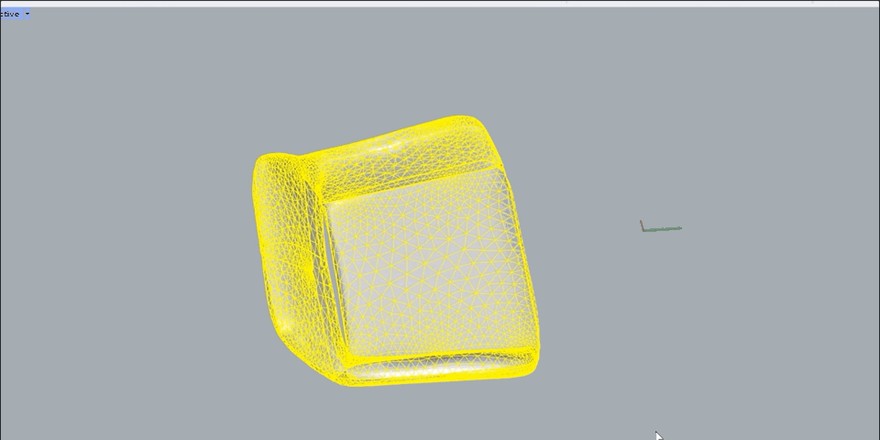
Шаг 4: Вывод dxf. Файлы раскроя
Система поддерживает форматы obj, stl, ply и другие, а также совместима с Solidworks, PRO/E и другими программными системами. Выведите файл раскроя в формате dxf, после чего обложка может быть изготовлена.
3D Flatten Seam Development – это комплексное решение для разворачивания 3D-моделей в 2D-листы кроя. С помощью 3D-сканера EinScan H компания Lea Tech значительно повышает эффективность процесса изготовления лекал и ускоряет время отклика при разработке продукции.
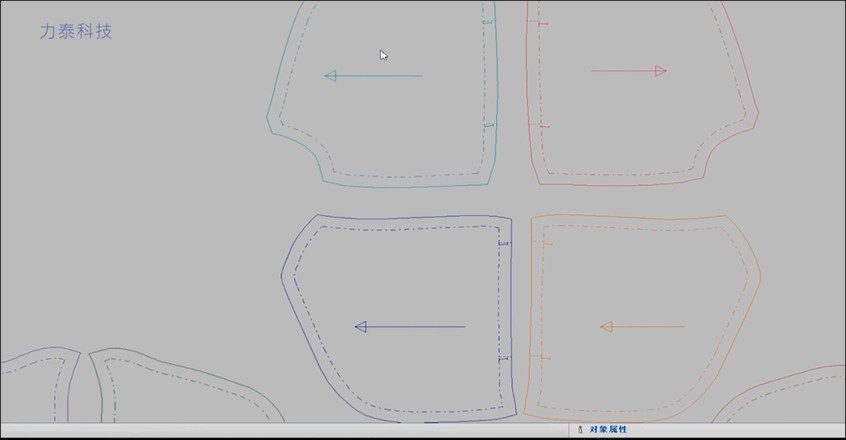
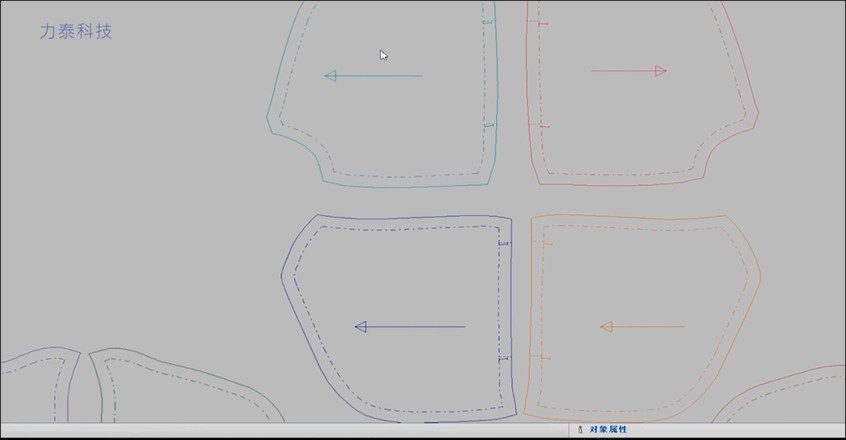